_Banner.jpg?ixlib=gatsbyFP&auto=compress%2Cformat&fit=max&q=50&w=2500&h=1251)
Business: Top Challenges in Manually Managing Warehouse Workers
Operational excellence in your warehouse can only be achieved if your workers are showing up to the right shifts, performing well in their day to day tasks, and adopting efficient ways of working to optimize their output.
However, oftentimes we see the opposite happening. Your workers do not show up to their assigned shifts. There’s a lot of miscommunication and human error in shift scheduling and attendance tracking. Warehouses miss their daily quotas due to high turnover rates.
What warehouse operations managers and HR managers often fail to realize is these are merely symptoms of one main problem: the lack of a seamless and efficient workforce management process. By relying on manual tools and legacy systems to manage your warehouse fleet, there could be issues in human error, miscommunication, and coordination bottlenecks that could snowball into low productivity, high turnover rates, and a loss in efficiency.
Create Free Business Account
Start hiring and managing your workforce today. Instantly create a business account to start your 30-day free trial. No obligation and no credit card required.
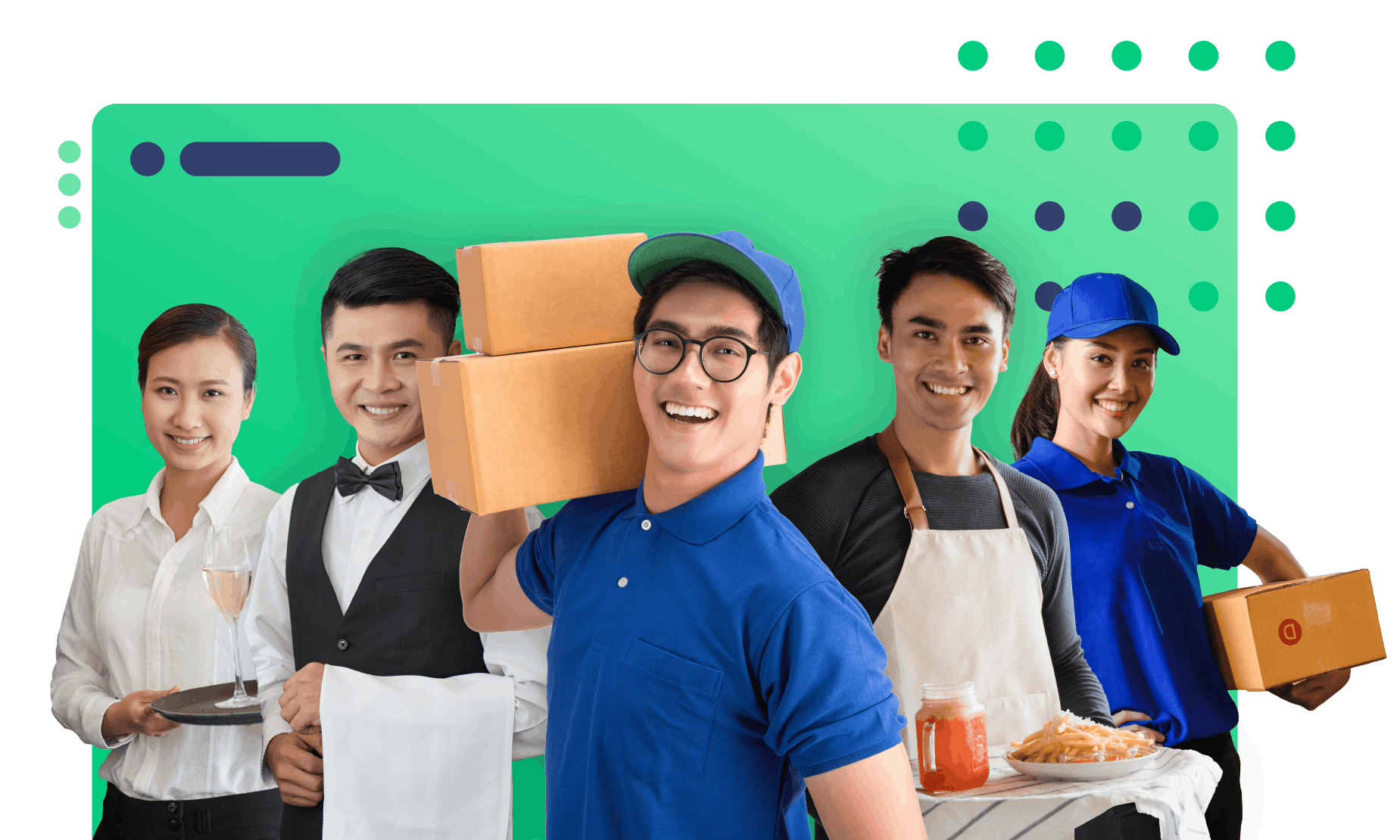
How does manual workforce management processes impact your warehouse productivity?
1. Inefficient flow of information due to disintegrated tools and systems
Inefficiencies in managing your workforce can be found in manual documentation and communication tools, such as:
- Manual shift scheduling, like using a spreadsheet
- Communication using SMS or short messages
- Time and attendance tracking using paper timesheets or google forms
Furthermore, these legacy tools and ways of working are not connected to each other. Shift schedules are found in one Excel spreadsheet- that gets sent out through a Whatsapp group message, and then workers record their attendances through another paper form on-site. This means that there is no seamless flow of information between the processes involved in managing and mobilizing your workforce, causing you to have to constantly check back and forth for the right information and spend hours on coordination and reconciliation.
In addition, records are left untraceable, and if lost or not updated in time, it will take a relatively long time for HR to perform an audit because all processes have been done manually.
2. Manual tools leave a lot of room for human error and inaccuracies
Beyond inefficiencies caused by fragmentation of tools and systems, these manual processes are also highly error-prone. Think about how many times your operations or HR managers have to edit or swap shifts around last minute- or how many paper timesheets are recorded across your various locations daily. Even if your staff and supervisors are trained regularly, there is still a huge opportunity for things to get missed along the way, causing inaccuracies that can be difficult to identify and resolve.
Inaccuracies in shift scheduling means workers do not know when to show up, potentially causing missed daily output targets for that day. Inaccuracies in timesheets mean workers could get paid the wrong amount, causing them to be disgruntled and churn. Errors are bound to happen with manual tools- especially if you are managing thousands of workers across different warehouse locations- and could have a significant impact on your operational efficiency.
3. Precious daytime wasted on tasks that yield low value
If you believe that “Time is Money”- then think of how much dollars are lost on HR teams doing manual coordination and timesheet reconciliation! Your ops team has to spend hours calling up workers to remind them of shift changes, and your HR team spend days looking at paper timesheets, trying to reconcile payroll. This means that the bulk of their working hours is spent on processes that could be automated and done in seconds, instead of doing work that can yield higher value for your business.
4. Delayed reports and lack of data on overall workforce performance
One of the biggest challenges with manual workforce management is the lack of timely data to track your warehouse performance. Reports on worker attendance, churn, and expenses spent on overtime usually come in bits and pieces, and offer no holistic or comprehensive view on what is happening on your warehouse floor. Often, data is one week or one month old, meaning the learnings are already outdated and you don’t have a chance to take action to optimize.
Furthermore, there is no robust way to collect feedback from your supervisors or your workers- causing HR teams to be left in the dark on how to optimize for better worker retention, engagement and productivity.
To solve these challenges that occur in manual processes, you can switch to the use of a digitized integrated system- the Workforce Management Platform.
A Workforce Management Platform enables you to automate management processes that would otherwise be error prone and time consuming. Here are a couple of things you can do on Workmate, the only workforce management platform specially designed for the blue collar workforce.
- Schedule and communicate shifts in a few clicks, with the confidence that workers will show up to the assigned shifts.
- Track time and attendance using a secure and accurate QR clock-in system, which automatically feeds into timesheets you can trust
- Cut down on time spent on timesheet reconciliation and approve hundreds of timesheets in seconds
- Integrate with your payroll so workers receive the right payments on time, increasing their morale and reducing worker turnover
- Collect feedback from supervisors on each workers ratings, to know who is performing well in your workforce
- See workforce attendance, performance, and expenses in real time- giving you the ability to quickly identify potential issues early on and know how to optimize in time
- Source reliable workers in a matter of hours each time you have to fill gaps in your workforce- with rich data that matches the right worker for the job
Workmate’s workforce management tools enable you to organize your workforce, seamlessly and accurately, improving shift attendance rates, better workforce performance and retention.
If you need additional workers, our integrated worker network is ready to fill any gaps in your workforce. Our AI-algorithm processes real historical data we have on worker attendance, performance, and ratings provided by previous employers- so you can be sure that workers are qualified and reliable.
Click here to create a free account and book a demo with our team.
To find out more about how to optimize for warehouse workforce efficiency, download our free E-book here.